Aluminum Casting for High Volume Production of Structural Nodes in BIW
Background Information
Environmental pollution can result from the passenger cars’ CO2 emissions. Therefore, the decline in these emissions, as shown in Fig.1, is regarded as an important and vital future requirement.
Decreasing the body in white’s (BIW) weight is considered as one of the solutions, which might have a great impact on the emissions’ reduction potential.
This weight reduction can be achieved by the integration of lightweight materials, such as Aluminum, in the vehicle body structures, in the form of castings.
In addition to the weight reduction potential of the Aluminum castings, function efficiency and easier assembly process might also be achieved.
Fig.2 provides an overview about the different BIW’s sections, which were considered as lightweight metal candidates within the multi material light weight (MMLV) vehicle project. From this figure, it is evident that shock towers, rear rails, torque boxes and hinge pillar reinforcements were regarded as good Aluminum castings’ candidates.
Aim of the project:
The main aim of this project is to be develop a cost efficient process route for the mass production of structural Aluminum body castings (500000 - 1000000 parts).
For the optimum process route to be reached, different aspects and factors have to be optimized.
Some of the considered factors include:
- The feeding material
- The heat treatment
- The casting process
- The Vacuum condition
Project Partners
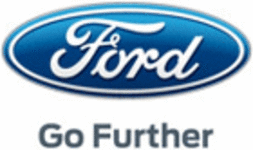
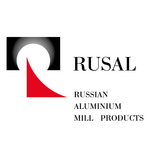
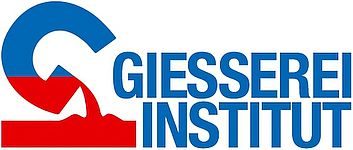